Exploring the 4 Major Categories of Welding Techniques
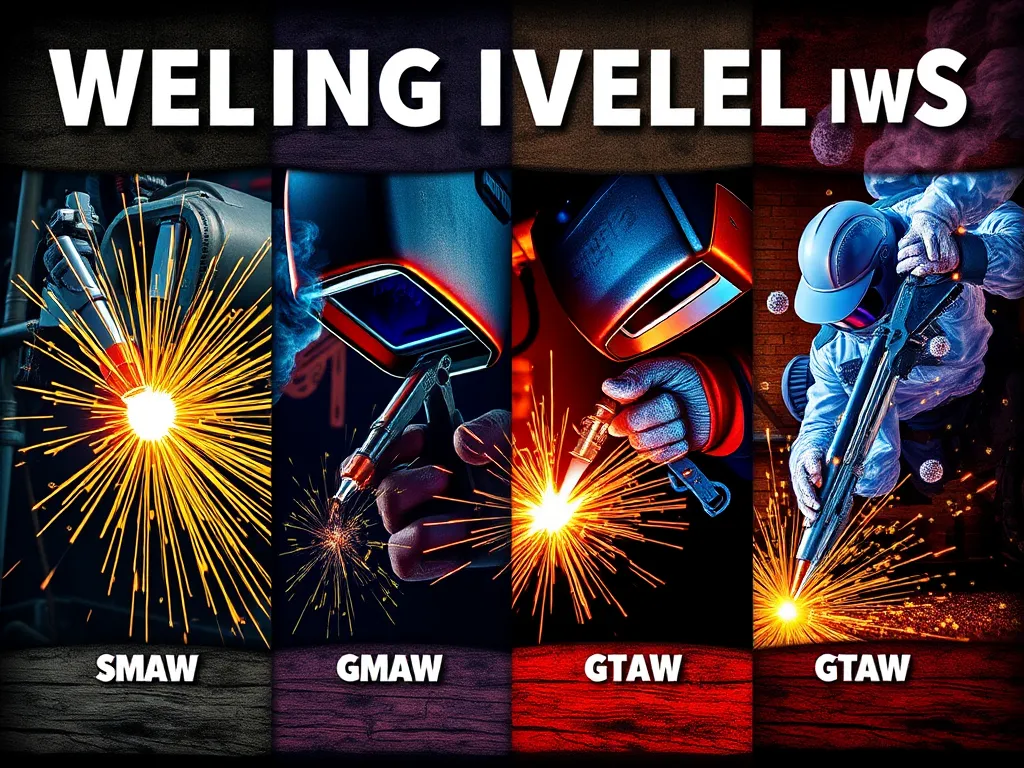
Welding: The Art and Science of Joining Materials
Welding is a vital process used in various industries to join materials, mainly metals, by applying heat, pressure, or both. This method creates a strong bond between two or more pieces, making it indispensable in construction, manufacturing, and repair services. Understanding welding techniques and their applications is essential for anyone involved in fabrication, engineering, or DIY projects.
The process of welding has evolved over the years, introducing new techniques and technologies that enhance its efficiency and effectiveness. Various welding methods cater to different materials and desired outcomes, including arc welding, gas welding, resistance welding, and energy beam welding. Each technique has its unique characteristics, advantages, and disadvantages, making it crucial to choose the right method for a specific application.
In the intricate dance between art and science, understanding the various Welding control categories is essential for achieving precision and durability in every project.
Welding safety is paramount, as the process involves high temperatures, harmful fumes, and potential injury risks. Proper equipment, protective gear, and safety protocols must be followed to ensure the well-being of the welder and those around them. Additionally, understanding the properties of the materials being welded is important for achieving optimal results and ensuring the integrity of the final product.
With the rise of automation and advanced technologies, welding has also embraced innovation. Automated welding systems and robotics are increasingly used in industrial applications, improving precision, productivity, and consistency. The future of welding will likely see further advancements in techniques and equipment, driven by the need for sustainable and efficient manufacturing practices.
In the intricate world of welding, mastering manual welding techniques not only enhances precision but also fosters a deeper connection between the welder and the materials being joined.
In conclusion, welding is a critical process that continues to play a significant role in modern society. Whether for construction, manufacturing, or artistic endeavors, mastering the art of welding opens up a world of possibilities for creators, engineers, and tradespeople alike.
Arc Welding
Arc welding is one of the most widely used welding techniques, leveraging an electric arc to generate heat. The primary forms of arc welding include Gas Metal Arc Welding (GMAW), Shielded Metal Arc Welding (SMAW), and Flux-Cored Arc Welding (FCAW). Each method has its specific applications, ranging from thin sheet metals to heavier structural components, making them versatile choices across various industries.
In today’s rapidly evolving industrial landscape, the integration of automated welding processes is transforming the way we approach the art and science of joining materials, ensuring precision and efficiency like never before.
Gas Metal Arc Welding (GMAW), also known as MIG welding, is a process that uses a continuous feed of filler metal and shielding gas to protect the weld pool from contamination. GMAW is favored for its speed and versatility, allowing for a clean and efficient welding process that is suitable for both beginner and experienced welders.
Shielded Metal Arc Welding (SMAW), commonly referred to as stick welding, involves using a consumable electrode coated with flux. When the electrode is struck against the base metal, an electric arc is formed, melting the electrode and creating a weld puddle. This technique is known for its simplicity and effectiveness in outdoor and windy conditions, although it requires a higher level of skill compared to GMAW.
Gas Welding
Gas welding, often associated with Oxy-Acetylene welding, utilizes a flame produced by burning a mixture of oxygen and acetylene. This method is traditionally used for brazing, soldering, and welding various metals. Its controllable heat output makes gas welding suitable for delicate tasks and thin materials, providing a significant degree of versatility.
Oxy-Fuel Welding is a gas welding process that employs a variety of fuel gases, including acetylene, propane, and hydrogen, alongside oxygen. This method is well-regarded for its portability and the ability to weld or cut metals using the same basic equipment, making it ideal for repair jobs and field applications.
Gas Tungsten Arc Welding (GTAW), commonly known as TIG welding, uses a non-consumable tungsten electrode to produce the weld. A filler rod may be added manually, and inert gas protects the weld area from atmospheric contamination. GTAW is known for delivering high-quality welds with precise control, making it the preferred choice for thin-walled sections and applications requiring a clean finish.
Resistance Welding
Resistance welding is a process that joins materials through the application of pressure and electric current. This technique is often used in industrial applications for its speed and efficiency. The most common forms of resistance welding include spot welding, seam welding, and projection welding.
Spot welding is a type of resistance welding that creates a weld at specific points on the workpieces. An electric current flows through the metal, generating heat at the contact points, which fuses the materials together. Spot welding is widely used in automotive manufacturing, where multiple sheets of metal need to be joined quickly and securely.
Seam welding is similar to spot welding but involves continuously welding along a seam to create a joint. This method is typically used for joining thin metal sheets in the production of vessels and tanks, ensuring leak-proof seams that can withstand pressure. Seam welding applications are common in the automotive and appliances industries.
Energy Beam Welding
Energy beam welding encompasses advanced techniques that utilize focused energy beams to create welds. This category includes Laser Beam Welding (LBW), Electron Beam Welding (EBW), and Plasma Arc Welding (PAW). These methods provide high precision and can be used for various applications, even in very thin materials.
Laser Beam Welding (LBW) uses highly focused laser beams to melt and fuse materials together. This technique is known for its speed and precision, making it ideal for intricate designs and applications in industries like aerospace, automotive, and electronics. LBW also offers deep penetration capabilities, reducing the need for multiple passes.
Electron Beam Welding (EBW) involves using a beam of high-velocity electrons to generate heat and join materials in a vacuum. This method allows for deep penetration and minimal thermal distortion, making it suitable for high-strength applications in industries such as aerospace and nuclear power. Plasma Arc Welding (PAW) is similar to GTAW but utilizes a plasma arc to enhance the melting process, providing versatility in joint design and material selection.