Essential Guide to Understanding the Basics of Arc Welding
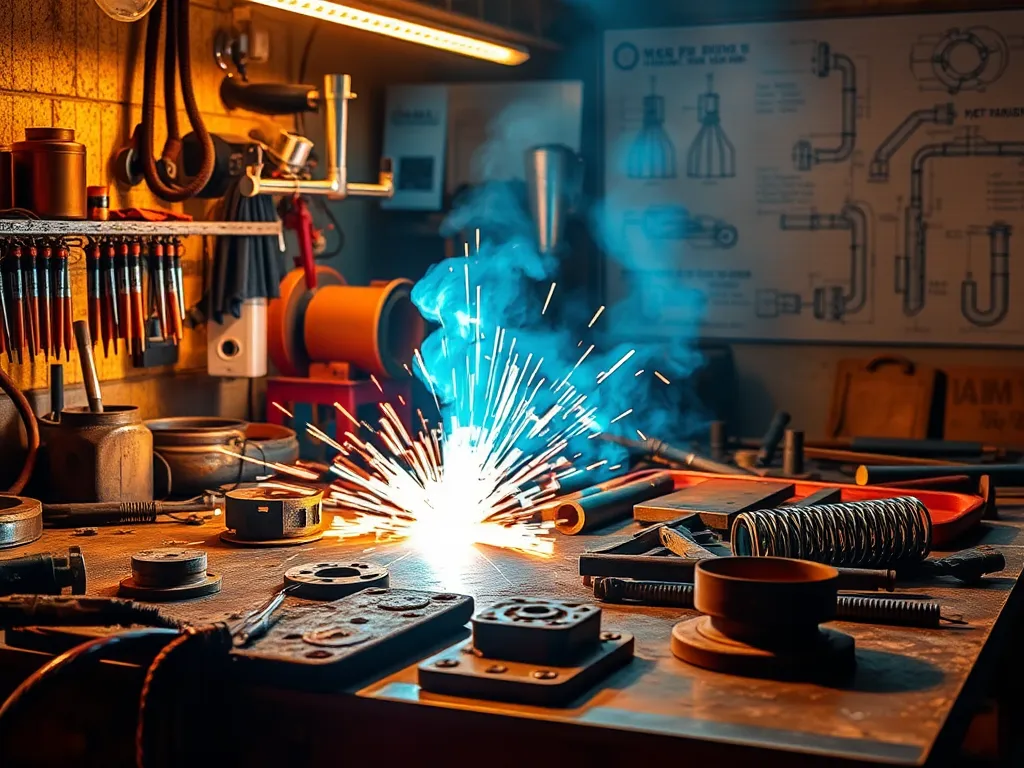
A Comprehensive Guide to Arc Welding
Arc welding is a versatile and widely-used welding process that involves the use of an electric arc to melt and join metals together. This technique is utilized across various industries and applications due to its effectiveness in producing strong, durable welds. The fundamental principle behind arc welding lies in creating an arc between an electrode and the workpiece, which generates enough heat to melt the base material and the filler metal, enabling a solid bond once cooled.
Exploring various metal fusion techniques can significantly enhance the quality and integrity of welding projects.
One of the most significant advantages of arc welding is its adaptability. The process can be performed in various positions and can work with a broad spectrum of materials, including steel, aluminum, and cast iron. Different arc welding methods also offer unique benefits; for instance, Shielded Metal Arc Welding (SMAW) is robust and portable, while Gas Metal Arc Welding (GMAW) or Metal Inert Gas (MIG) welding is known for its speed and ease of use. Understanding these variations is crucial for selecting the appropriate technique based on the project's requirements.
The electrical arc process is a critical method utilized in modern welding applications, ensuring strong and durable joints.
Safety is an essential aspect of arc welding, as the process involves high temperatures and electrical hazards. Proper training and adherence to safety protocols are vital to minimize risks. Personal Protective Equipment (PPE) such as welding helmets, gloves, and protective clothing should always be worn to safeguard against sparks, heat, and ultraviolet rays emitted during welding. Moreover, understanding the electrical parameters and maintaining equipment plays a significant role in ensuring successful and safe welding operations.
Understanding arc welding fundamentals is essential for anyone looking to excel in welding techniques.
As industries continue to evolve, the applications of arc welding are extensive, ranging from construction and manufacturing to artistic endeavors and repairs. In construction, arc welding facilitates the joining of steel structures, ensuring stability and strength. In manufacturing, this technique is used extensively in creating products such as automobiles and heavy machinery. Moreover, artists have embraced arc welding as a medium for creating intricate sculptures and installations. Its versatility allows for innovation across various fields.
In conclusion, arc welding is a fundamental process in modern fabrication and construction, promoting efficiency and strength in metal joining. By understanding the various techniques, safety precautions, and applications of arc welding, professionals can enhance their skills and expertise, contributing to high-quality projects in diverse industries.
Fundamentals of Arc Welding
Arc welding is defined as a process that uses a welding power supply to create an electric arc between an electrode and the base material, resulting in the melting and fusion of metals. This process can utilize several techniques, including shielded metal arc welding (SMAW), gas metal arc welding (GMAW), and gas tungsten arc welding (TIG), each serving different applications and material types.
There are various types of arc welding processes, including SMAW (Shielded Metal Arc Welding), GMAW (Gas Metal Arc Welding), and GTAW (Gas Tungsten Arc Welding), among others. Each process has unique characteristics that make it suitable for different materials and applications. For instance, SMAW is known for its portability and ease of use, while GMAW offers a cleaner weld with minimal cleanup due to the use of a shielding gas.
The basic welding equipment needed for arc welding includes a welding power supply, electrodes, and various safety gear. The welding power supply can be either AC or DC, depending on the welding technique being employed. The electrodes are responsible for providing the necessary filler material and current to create the arc. In addition, personal protective equipment, such as welding helmets, gloves, and protective clothing, is essential for ensuring the safety of the welder.
Understanding welding electrical parameters is crucial in arc welding. Key parameters include voltage, current, and travel speed, which directly impact the quality of the weld. For instance, higher voltage can lead to a wider bead but may also increase the risk of burn-through on thinner materials. Therefore, it is essential to adjust these parameters based on the specific materials and conditions being welded.
Arc Welding Techniques
SMAW (Shielded Metal Arc Welding) is a manual arc welding process where an electric arc is established between a coated electrode and the base metal. This technique is highly versatile and can be used for welding in various positions. The electrode coating provides a shielding gas and slag that protect the molten weld pool from contamination. It is especially advantageous for outdoor applications, as it is less affected by wind and environmental factors.
GMAW (Gas Metal Arc Welding), also known as MIG (Metal Inert Gas) welding, utilizes a continuous wire feed as the electrode, along with a shielding gas to protect the weld from atmospheric contamination. This automated approach increases speed and efficiency in the welding process, making it a popular choice in manufacturing. GMAW is ideal for thin to medium-thickness materials and offers a clean and high-quality weld.
TIG (Gas Tungsten Arc Welding) welding employs a non-consumable tungsten electrode to produce the weld. Unlike SMAW and GMAW, TIG requires a separate filler material added to the weld pool. This technique allows for precise control over the welding process, making it suitable for applications that demand high-quality welds, such as aerospace and artistic applications. TIG welding is versatile and can be performed on a wide range of materials, including stainless steel and aluminum.
Welding positioning techniques are crucial for achieving optimal results in arc welding. Proper positioning can influence the quality and strength of the weld. The common welding positions include flat, horizontal, vertical, and overhead. Each position presents unique challenges, and welders must adapt their technique, travel speed, and equipment settings to ensure consistent and high-quality welds across different orientations.
Safety in Arc Welding
Personal Protective Equipment (PPE) for welding is essential for ensuring the safety of the welder. This equipment includes a welding helmet with a proper tint to protect against ultraviolet and infrared radiation, gloves made from heat-resistant materials, and protective clothing that covers the skin. Additionally, safety shoes and ear protection may be necessary in certain environments. Wearing PPE reduces the risk of burns, eye injuries, and inhalation of harmful fumes.
Electrical safety precautions are critical when performing arc welding. First and foremost, the welding machine should be correctly grounded to prevent electric shock. Welders must be trained in recognizing potential hazards, such as frayed cables or damaged equipment. Furthermore, isolating the welding area from unintended personnel can minimize risks. Awareness of electrical safety protocols is vital in ensuring a safe working environment for all.
Fire hazards in welding are a significant concern due to the high temperatures generated during the welding process. Sparks and molten metal can ignite flammable materials nearby, causing serious accidents. Therefore, it is essential to maintain a clean working environment, free from combustible materials. Using fire-resistant barriers or curtains and having fire extinguishing equipment on hand can further mitigate fire risks during welding operations.
Ventilation and fume management are critical aspects of arc welding safety. Fumes emitted during welding can be harmful if inhaled. Proper ventilation ensures a continuous flow of fresh air, reducing the concentration of harmful fumes in the workspace. Local exhaust ventilation systems or fume extraction equipment can be employed. Additionally, welders should be educated on fume composition generated during welding to take necessary precautions.
Applications of Arc Welding
Industrial applications of arc welding are vast and include sectors like automotive, shipbuilding, rail transport, and heavy machinery manufacturing. In these industries, arc welding offers efficient metal joining solutions, essential for building robust structures and components. The ability to weld various metals and alloys makes arc welding suitable for many applications, ensuring reliability and strength in finished products.
In construction and structural applications, arc welding is fundamental in joining steel beams, reinforcing bars, and other structural components. This technique ensures strength and longevity in buildings, bridges, and other infrastructure projects. The flexibility and reliability of arc welding techniques allow construction professionals to adapt to different design requirements while meeting safety and quality standards.
Artistic uses of arc welding are increasingly popular, with artists utilizing welding techniques to create sculptures and installations. The ability to manipulate metal through welding allows artists to explore innovative designs and concepts. Arc welding provides a unique medium for artistic expression, where the raw and industrial nature of the materials can be highlighted in the final artwork.
Repair and maintenance welding are essential for extending the life of equipment and structures. Arc welding is commonly employed in repairing machinery, vehicles, and infrastructure. By effectively addressing wear and damage, welders can restore the functionality of components, saving costs associated with replacements and ensuring continued operation in various industries.
Troubleshooting Arc Welding
Common welding defects include porosity, undercutting, and incomplete fusion, which can compromise the integrity of the weld. Understanding the causes of these defects, such as improper technique, incorrect settings, or contamination, is crucial. Welders can utilize various methods to identify and resolve issues, including adjusting settings or changing equipment to ensure high-quality welds.
Adjusting welding parameters is an essential skill for welders to produce consistent results. Parameters such as voltage, current, and travel speed must be fine-tuned based on the type of material and thickness being welded. Regularly monitoring and adjusting these parameters can help prevent defects and enhance the overall quality of the weld. Training and experience are vital in mastering these adjustments.
Maintaining welding equipment is necessary for ensuring safe and effective welding operations. Regular inspections for wear and tear, cleaning of nozzles and contact tips, and proper storage of equipment can prolong the life of welding tools. Additionally, proper calibration of the welding machine is essential for maintaining consistent performance and preventing malfunctions during welding tasks.
Identifying arc welding problems involves being attentive to several indicators, such as irregular arc behavior, inconsistent bead appearance, or overheating of components. Regularly assessing the welding process and the condition of the equipment can help welders proactively address problems before they become severe. Knowledge of common issues and their solutions is invaluable for maintaining productivity and quality in arc welding.