Discovering TIG Welding: Techniques, Benefits and Tips
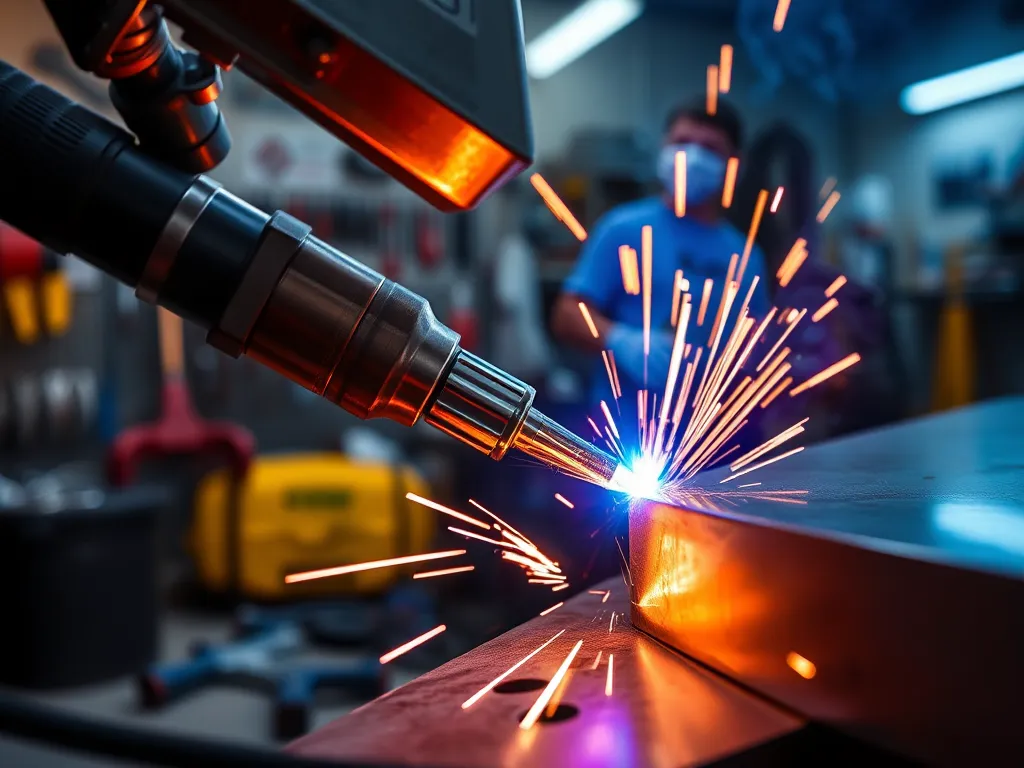
Understanding TIG Welding: A Comprehensive Guide
TIG Welding, or Tungsten Inert Gas Welding, is a versatile and high-quality welding process that is widely used in various industries for its precision and control. Unlike other welding methods, TIG welding utilizes a non-consumable tungsten electrode to produce the weld, ensuring cleaner and more precise welds with minimal spatter. This technique makes it particularly suitable for thin materials and applications where strong weld integrity is crucial.
For professional tig welding services, contact our experts.
The process involves forming an arc between the tungsten electrode and the workpiece, which melts the material together with a filler rod if necessary. TIG Welding is known for its ability to weld a wide variety of metals, including steel, stainless steel, aluminum, and magnesium, making it an essential skill for welders of all levels. It requires a higher level of skill and practice compared to other methods, but the quality of the finished product is often worth the investment in training.
Through ongoing advancements in technology and techniques, TIG welding has evolved to become more efficient and user-friendly. The introduction of inverter technology, for example, has significantly improved the flexibility and portability of TIG welding equipment. This modernization has made TIG welding more accessible to newcomers while still satisfying the demands of experienced professionals looking for precision in their work.
Overall, the importance of TIG Welding cannot be overstated in today’s manufacturing and construction industries. Its ability to produce strong, clean welds makes it the go-to choice for applications that require high structural integrity and aesthetics. As industries continue to evolve, the demand for skilled TIG welders will remain high, ensuring that this technique will play a vital role for years to come.
Our certified tig welder is ready to assist with your project.
In conclusion, TIG Welding is an essential welding technique that provides numerous benefits, including precision, versatility, and the ability to work with a wide range of metals. Whether you are a novice welder or an experienced professional, understanding the principles and techniques of TIG welding is key to excelling in this craft.
TIG Welding Basics
TIG Welding, also known as Gas Tungsten Arc Welding (GTAW), is defined as a welding process that uses a non-consumable tungsten electrode to produce the weld. The welding arc is formed between the tungsten electrode and the base material, which is protected by an inert gas, typically argon, to prevent contamination. This process can be used with or without a filler rod depending on the specific requirements of the weld.
If you're wondering what is tig welding, our website offers a comprehensive guide.
TIG welding technology has its roots in the 1940s, primarily developed during World War II for aircraft manufacturing. The need for reliable, high-strength welds in aircraft structures led to the innovation of this technique, which allowed for precision welding in hard-to-reach areas. Over the following decades, TIG welding improved significantly with advancements in equipment and techniques, and it became popular across various industries, including automotive and construction.
The key components of TIG welding equipment include the power source, the welding torch, the tungsten electrode, the gas supply, and the filler material. The power source delivers the required electrical current, while the welding torch houses the tungsten electrode and directs the flow of inert gas. The filament diameter and type of tungsten electrode used can vary based on the thickness and type of material being welded, making it crucial for welders to select the appropriate components for their specific projects.
Techniques in TIG Welding
Setting up TIG welding equipment involves several steps: selecting the correct tungsten electrode, preparing the workpiece, adjusting the power settings, and ensuring a consistent flow of inert gas. It’s essential to clean the surface of the materials to be welded, as contaminants can affect the integrity of the weld. The welder should also adjust the amperage according to the material thickness, which can significantly impact the quality of the weld.
Different materials require different welding techniques in TIG welding. For example, stainless steel may require a different amperage setting and filler metal compared to aluminum or magnesium. Welders must adapt their techniques to accommodate variations in melting points and chemical properties of the metals being worked with. Using the appropriate filler material and maintaining a stable arc are also crucial in achieving successful welds across diverse materials.
Common mistakes in TIG welding include inconsistent travel speed, improper tungsten electrode angles, and inadequate cleaning of the base material. To avoid these issues, welders should practice maintaining a steady hand, ensuring the correct arc length, and regularly cleaning the work surface. By developing strong foundational techniques and understanding common pitfalls, TIG welders can improve their skill level and achieve better results in their projects.
Advantages of TIG Welding
The primary benefits of using TIG welding in projects are the high-quality welds it produces, the versatility in welding various metals, and the minimal spatter created during the process. These factors make it ideal for projects that require clean aesthetics or require welding thin materials, such as those found in aerospace or artistic metalwork. The precision offered by TIG welding also reduces the need for post-weld cleanup, saving time and resources.
When compared to other welding methods, such as MIG welding or stick welding, TIG welding stands out for its ability to produce stronger, more reliable welds. While MIG welding is typically faster and easier for beginners, TIG welding gives greater control over the weld pool and allows for welds in more challenging positions. This offers a distinct advantage for projects where precision and quality are paramount.
TIG welding is utilized across various industries, including aerospace, automotive, construction, and manufacturing. Its applications range from creating structural components in aircraft and vehicles to fabricating delicate artwork or medical equipment. Industries that prioritize high-quality welds often depend on TIG welding due to its strengths in producing reliable and aesthetically pleasing results.
TIG Welding Safety Tips
Essential safety gear for TIG welding includes protective gloves, a welding helmet with appropriate shading, flame-resistant clothing, and proper ventilation in the workspace. A welding helmet is crucial to shield the eyes from harmful ultraviolet light emitted during the welding process. Gloves should be made from materials that can withstand heat and provide dexterity while handling the welding torch and filler material.
Best practices for safe TIG welding involve continuously monitoring your surroundings, ensuring proper ventilation to avoid inhaling harmful fumes, and maintaining a clean workspace by removing any flammable materials. Understanding the functions of your equipment, performing regular maintenance, and following safe operational procedures can significantly reduce the likelihood of accidents or injuries.
Common hazards in TIG welding include electrical shock, exposure to harmful gases, and burns. To mitigate these risks, welders should be well-trained, use equipment properly, and follow safety protocols at all times. Employing a buddy system to have someone nearby can also enhance safety, particularly in industrial environments where additional risks may be present.
TIG Welding Projects
For beginners, TIG welding project ideas can include making simple joints or fabricating small items like brackets or custom frames. These projects allow novice welders to practice their skills in control, travel speed, and developing a consistent weld. Completing these smaller projects builds confidence and provides a foundation for more complex welding tasks.
Advanced TIG welding techniques for skilled welders may include working with exotic materials, creating complex fabrications, or performing intricate design work. Experienced welders may also take on challenges such as welding in tight spaces or achieving welds on different angles. The ability to master these advanced techniques elevates a welder's expertise and sets them apart in the field.
Choosing the right TIG welding project for practice involves assessing your skill level, available materials, and equipment. Beginners should select projects that are manageable and focus on developing fundamental skills, while more experienced welders may choose projects that stretch their capabilities and tackle new challenges. Ultimately, selecting a project that aligns with your interests and goals will provide a more rewarding learning experience.