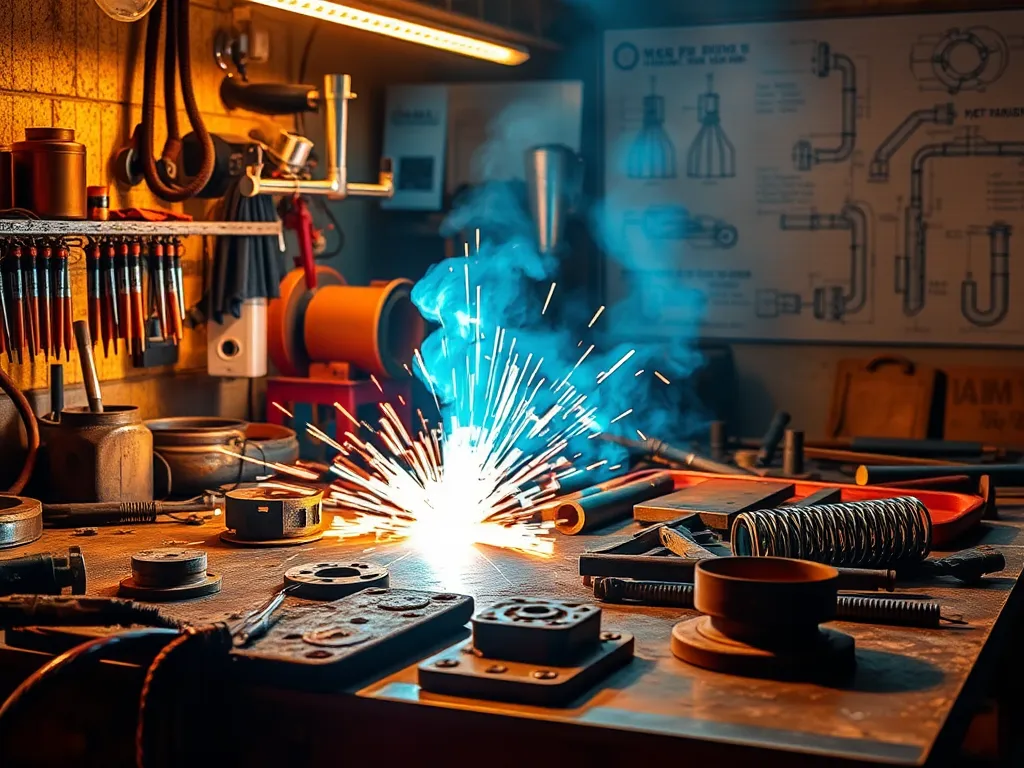
Essential Maintenance Tips for Mobile Welding Machines
Key Takeaways
- Significance of consistent upkeep for welding equipment
- Crucial care advice for portable welding devices
- Optimal methods for welding machinery maintenance
- Selecting the appropriate welding apparatus for your requirements
- Particulars of welding machines in KSA
- Diagnosing frequent problems in welding machines
Importance of Regular Maintenance for Welding Machines
Regular maintenance is crucial for ensuring the optimal performance and longevity of welding machines. Implementing effective maintenance tips for mobile welding machines can significantly reduce the risk of unexpected breakdowns and enhance safety for welders. Proper care not only extends the life of the equipment but also improves the quality of welding processes, whether through mig welding, stick welding, or more specialized techniques like autogenous welding and orbital welding. Regular checks, such as inspecting welding helmets and monitoring for welding fumes, help in identifying issues before they escalate. By prioritizing maintenance, operators can achieve consistent results and maintain high standards in their work, ensuring that every weld meets the required specifications.
Maintenance Task | Frequency | Description |
---|---|---|
Inspect Welding Cables | Weekly | Check for any signs of wear, fraying, or damage to ensure safety during operation. |
Clean Welding Machine | Daily | Remove dust and contaminants to prevent overheating and ensure efficient operation. |
Check Gas Levels | Before Each Use | Make sure that gas tanks are filled to avoid interruptions during welding operations. |
Inspect Safety Gear | Monthly | Ensure welding helmets, gloves, and protective clothing are in good condition to maintain safety standards. |
Perform Equipment Calibration | Quarterly | Regularly calibrate welding machines to ensure precise settings and high-quality welds. |
Benefits of Proper Care
Proper maintenance is essential for all types of welding machines, including stick welders, tig welders, and mig welders. Regular care helps ensure optimal performance during the fabrication process. Preventive maintenance can reduce the likelihood of unexpected breakdowns, allowing operators to focus on their tasks without interruption. Following maintenance tips for mobile welding machines can help extend the life of the equipment, keeping the wiring and other components in good condition.
Routine maintenance not only enhances the efficiency of the machines but also improves the quality of the welded joints. A well-maintained tig welder will produce cleaner and more precise welds, which is crucial for high-quality fabrication work. Taking the time to adhere to effective maintenance practices can lead to significant cost savings in the long run, as repairs and replacements become less frequent. Following comprehensive maintenance tips for mobile welding machines demonstrates commitment to safety and quality in welding operations.
How Maintenance Extends Equipment Lifespan
Regular maintenance plays a crucial role in extending the lifespan of welding machines. By following effective maintenance tips for mobile welding machines, technicians can ensure that equipment operates efficiently. Regular inspections help identify potential issues before they escalate into costly repairs. Proper care not only enhances weld quality but also safeguards the integrity of materials like stainless steel during fabrication. Without routine upkeep, grinding tools and soldering equipment may wear prematurely, leading to frequent breakdowns and repair needs.
Investing time in maintenance also contributes to safety in the workplace. Technicians are less likely to encounter unexpected failures when machinery has been properly maintained. Wearing safety glasses is essential during inspections to protect against debris and sparks. By prioritizing maintenance tips for mobile welding machines, users can create a safer environment while extending the functional life of their tools. This proactive approach ensures that welding equipment remains reliable, ultimately minimizing downtime and enhancing productivity.
Essential Maintenance Tips for Mobile Welding Machines
Regular maintenance is crucial for ensuring the optimal performance of welding machines, particularly in mobile applications. Implementing maintenance tips for mobile welding machines can significantly enhance their reliability and longevity. A daily inspection checklist should include checking the fuel filter, which prevents clogs and ensures the engine runs smoothly. Keeping the welding equipment clean, including wiping steel surfaces and ensuring no metal shavings accumulate, is essential for functionality. Inspect the oven for proper temperature settings and ensure that shielding gas levels are adequate to prevent defects. Don't overlook the importance of using quality filler metals, as these directly influence the weld quality. Following the manufacturer’s guidelines and adhering to maintenance tips for mobile welding machines can minimize the need for welding machine rental due to unexpected breakdowns.
Daily Inspection Checklist
Regular inspections are crucial for ensuring the reliability of your welding equipment. Implementing daily maintenance tips for mobile welding machines can help identify potential issues early. A checklist should include checking the functionality of stick welding machines, examining the condition of cables, and confirming that all connections are secure. By closely monitoring general welding equipment, operators can prevent breakdowns during critical welding projects or jobs. Consistent attention to detail can make a significant difference in the efficiency of mechanized welding processes.
Maintaining welders requires a focus on essential components. Inspecting gas levels, ensuring proper electrode alignment, and checking for leaks are key aspects of welder maintenance. Operators should also verify that the right welding machine is used for specific welding work to achieve the best results. For those using KSA welding machines, reviewing unique features during inspections can aid in prolonging equipment life. By adhering to these practices, welders can sustain optimal performance for their ongoing welding services and ensure the success of their welding projects.
Weekly and Monthly Maintenance Tasks
Regular welder maintenance is essential for maintaining optimal welding performance and ensuring trouble-free welding during every project. Weekly maintenance tasks should include checking the integrity of cables and connections, inspecting the gas supply, and cleaning the welding nozzle to prevent any build-up that could lead to welding errors. For welding professionals, adhering to these maintenance tips for mobile welding machines can significantly enhance the quality of work produced, resulting in successful welding outcomes.
Monthly maintenance requirements go a step further, focusing on comprehensive checks of the arc welding machine. This includes inspecting the internal components, ensuring all electrical connections are secure, and calibrating settings to meet specific project needs. Keeping an eye on these machine maintenance tasks not only guarantees good welding power but also greatly extends the life of the equipment. Consistent attention to these details fosters a reliable performance and minimizes downtime due to unexpected failures.
Best Practices for Welding Machine Care
Effective machine maintenance is crucial to ensure optimal performance and longevity of various welding equipment, such as flux-cored welding machines and portable welders. Regularly checking welding cables and the welding gun cable can prevent inconsistent welding, which may lead to increased welding expenses. Utilizing maintenance tips for mobile welding machines can help welding operators identify issues early, ensuring that equipment like orbital welding equipment remains in peak condition. A commitment to proper machine maintenance not only enhances precision GTAW welding but also reduces the risk of costly repairs down the line. Implementing these best practices ensures you maximize the efficiency and reliability of your welding machinery.
- Regularly inspect and clean welding cables to prevent wear and tear. For any mobile welding scottsdale work contact Xpress mobile welding Phoenix.
- Check and tighten electrical connections to ensure proper conductivity.
- Monitor gas flow levels and replace gas cylinders as needed.
- Keep the welding machine and work area free of debris and clutter.
- Schedule routine maintenance checks with a qualified technician.
- Store the welding equipment in a dry, secure location when not in use.
- Use appropriate protective gear to maintain safety during maintenance tasks.
Cleaning Your Welding Equipment
Proper cleaning of your welding equipment is crucial for maintaining its efficiency and longevity. A good welder understands that flux-cored welding and wire welders can accumulate contaminants that affect performance. Regularly removing slag, spatter, and dust not only ensures a clear path for welding but also helps to identify potential maintenance problems early on. Incorporating these cleaning habits into your routine maintenance tasks will save you time and money on repairs down the line.
For those using high-tech TIG welders, specific repair techniques and detailed maintenance tips for mobile welding machines become even more vital. Conducting a full machine inspection during cleaning will allow you to spot wear and tear before it escalates, ensuring your welding equipment operates at peak performance. Whether you are a professional welder or a hobbyist, keeping your welding gear spotless and well-maintained is essential for achieving quality results and extending the life of your right welder.
Proper Storage and Transportation
Storing and transporting welding machines properly is a critical maintenance task that can greatly affect their longevity and performance. For instance, a small MIG welder should be kept in a dry, temperature-controlled environment to prevent damage to mechanical parts and sensitive electronics. A well-structured maintenance program that includes specific storage guidelines ensures that the machine remains in optimal condition. Neglecting these storage practices may lead to machine failure or necessitate costly electronics repair down the line.
Ensuring proper transportation of welding machines also plays a vital role in their maintenance. Lifting and securing machines correctly prevents physical damage during transit, which can directly impact weld quality. Using a weld quality monitor during operation helps to assess any potential issues caused by improper handling. Adhering to these maintenance tips for mobile welding machines not only enhances performance but also prolongs service life, ensuring consistent weld quality over time.
Choosing the Right Welding Machine for Your Needs
Selecting the right welding machine involves understanding your specific requirements for projects, especially in mobile welding situations. Consider features like weld terminals and weld cables, which play a crucial role in achieving high-quality welds. For tasks involving metal construction, a flux-cored welder may be more suitable due to its efficiency and versatility. Evaluating the specifications of the equipment is essential, as it can dictate how well it performs under various conditions and influences the maintenance needed. Adopting effective Maintenance Tips for Mobile Welding Machines can help ensure that both basic machine upkeep and major maintenance activities are addressed, prolonging the lifespan of your machine. A thorough maintenance plan will not only keep the weld circuit functioning properly but also enhance the quality of your welding projects.
Welding Machine Type | Best For | Features | Weight | Price Range |
---|---|---|---|---|
Flux-Cored Welder | Metal Construction | Efficiency, Versatility | 50 lbs | $200 - $600 |
MIG Welder | General Fabrication | Easy to Use, Fast Welding Speeds | 70 lbs | $300 - $800 |
TIG Welder | Precision Welding | High Control, Clean Welds | 40 lbs | $500 - $2000 |
Stick Welder | Outdoor Work | Portability, Low Cost | 30 lbs | $150 - $500 |
Evaluating Machine Specifications
Understanding machine specifications is crucial for ensuring that your welding tasks are performed efficiently and safely. High-quality equipment can make a significant difference in achieving a high-quality weld. Evaluating the specifications helps identify the machine's capabilities and limitations. Regular maintenance, including day-to-day maintenance and implementing preventive maintenance measures, can prevent equipment malfunction. Knowing the right specifications allows for timely adjustments, such as tightening weld terminals, which can help avert costly repairs down the line.
The importance of aligning machine specifications with your project needs cannot be overstated. A well-constructed preventive maintenance program will address the various equipment components that require routine checks and repairs. This proactive approach keeps the machine performing optimally and extends its lifespan. By carefully evaluating specifications, welders can select equipment that minimizes the risk of repair issues while ensuring the demands of their work are met effectively. Utilizing comprehensive Maintenance Tips for Mobile Welding Machines will aid in maintaining equipment reliability and performance.
Factors to Consider for Portable Welding
Evaluating the right portable welding machine involves understanding how maintenance impacts its longevity and performance. Regular preventive maintenance actions help identify issues before they escalate. Being aware of the heat generated by machines is essential for ensuring that metal parts function optimally. Working closely with the equipment manufacturer can provide insights into specific maintenance tips for mobile welding machines tailored to the actual equipment being used. Following complete maintenance checklists and adhering to a routine maintenance schedule are critical for maximizing the maintenance benefit.
Choosing a portable welding machine also requires attention to the tools needed for effective upkeep. Machines often encapsulate components that require little maintenance but still necessitate attention. Regularly inspecting the inside of the equipment and ensuring proper care can significantly improve performance. Keeping a well-organized set of maintenance tips for mobile welding machines can facilitate easy access to important guidelines. Ultimately, the right approach to maintenance can enhance both the efficiency and durability of your portable welding solutions.
Specifics of KSA Welding Machines
KSA welding machines offer unique features that cater to a range of applications, requiring specific attention during maintenance. Essential maintenance tips for mobile welding machines include performing basic inspections, such as ensuring proper cable inspect wire and assessing the integrity of vital machine elements. A professional technician should conduct a comprehensive weld head check to verify that all components function efficiently. Using a specialized cleaning solution aids in removing any residue and sparks that could affect performance. Regular technician check-ups are crucial for spotting potential issues before the next weld, ensuring reliability and safety during operation. Following proper safety precautions during maintenance will further enhance the longevity and efficiency of KSA models, particularly for those considering machine rental options.
Unique Features of KSA Models
KSA models are designed with advanced technology that enhances the welding process, ensuring strong welds and consistent performance. The integration of durable materials improves the overall longevity of the equipment. Regular maintenance, including routine checks and following the engine manual, is crucial. Users should prioritize inspecting drive rollers and addressing issues like cracked cables to avoid bad welds and the need for extensive rework. Utilizing proper tools, such as an insulated screwdriver, can further enhance the safety and efficiency of these machines.
These models also feature compatibility with various industrial supplies, making them versatile for different welding applications. For operators, implementing specific maintenance regimen recommendations is vital for optimal performance. This includes using quality steel electrodes and adhering to Maintenance Tips for Mobile Welding Machines. Following these guidelines helps ensure that welding tasks are completed efficiently, reducing downtime and maximizing productivity.
Maintenance Recommendations for KSA Equipment
Regular maintenance is crucial for KSA equipment to ensure its reliability and longevity. Operators should adhere to essential maintenance tips for mobile welding machines, including the inspection of connections and checking for damaged cables. A thorough examination of components such as the gas hose is vital, as a defective gas hose can pose a safety risk. Rusty areas should be promptly addressed to prevent further deterioration, while protective sleeves can help safeguard important parts from wear.
For optimal performance, the controller work must be consistently tested to identify any potential issues early. Steel drive rolls should be kept clean and free of debris to function efficiently, as neglect can lead to significant maintenance concerns. Using stainless steel components can enhance durability, ensuring that your equipment stands the test of time. Proper equipment care and regular checks will ultimately contribute to the overall performance and longevity of KSA welding machines.
- Regularly clean the equipment to remove dirt and debris.
- Schedule routine inspections to identify wear and tear before they become serious issues.
- Lubricate moving parts as recommended by the manufacturer to reduce friction.
- Replace worn or damaged parts promptly to maintain efficiency.
- Keep an organized maintenance log to track service dates and repairs.
- Ensure proper training for operators to recognize maintenance needs and safety practices.
- Follow manufacturer's guidelines for maintenance schedules and procedures.
Troubleshooting Common Issues in Welding Machines
Identifying and resolving common issues in welding machines requires a systematic approach. Regularly inspect the weld head and gun contact tips for signs of damage, ensuring they are free from wear that could impact performance. Always follow the manufacturer’s instructions for troubleshooting specific problems, as this can save time and resources. Ensuring that there is enough filler wire is crucial, as insufficient material can lead to weak welds. Regularly check protective covers to keep dust and debris away from sensitive components. Employing maintenance tips for mobile welding machines can enhance efficiency and reduce the likelihood of issues arising during operation.
Conclusion
Regular maintenance of welding machines ensures optimal performance and enhances safety during operations. Essential maintenance tips for mobile welding machines include a daily inspection checklist that emphasizes the importance of cable inspecting wire and conducting basic inspections of machine elements. Technicians should check the weld head and other components to prevent any sparks or accidents while preparing for the next weld. Utilizing a specialized cleaning solution can keep the equipment in top shape, while adhering to safety precautions during these tasks is critical. For those utilizing machine rental options, understanding and implementing these maintenance tips is vital for preserving the integrity of the welding equipment and achieving professional results.
FAQS
What are some common machine maintenance requirements for welding job performance and how can they affect weld quality?
To ensure trouble-free welding performance, it's essential to adhere to common welder maintenance practices. Regularly inspect connections and drive rollers, and make it a point to tighten weld terminals. By following these machine maintenance requirements, you can improve the consistency of welds and enhance equipment longevity. Keep in mind that machines generate heat, so proper system maintenance is crucial to maintain high-quality welds and avoid potential issues. For detailed guidance on equipment care, refer to resources provided by Kanoo Machinery.
How can proper equipment care for mobile welding machines enhance the quality of welds produced during a welding job?
Proper equipment care significantly affects weld quality by ensuring that stick welding equipment and arc machines operate efficiently. Regularly inspecting drive rollers and inside equipment helps maintain consistent welds and supports the creation of high-quality welds. By learning about the specific care required, a welder can improve the overall performance of their welding job and achieve better results.
How does the equipment care for mobile welding machines play a role in ensuring a high quality weld?
Proper equipment care is essential as it directly affects weld quality. To maintain high quality welds, one should inspect drive rollers regularly and ensure that the machine isn’t experiencing wear and tear. By implementing these maintenance practices, you can significantly enhance the performance of your welding job.
How does effective equipment care for mobile welding machines affect the overall performance of welding jobs?
Effective equipment care is essential as it directly affects weld quality. To ensure optimal performance during welding jobs, it is important to learn about and implement proper maintenance practices. This includes regular inspections and cleaning to prevent issues that could compromise the weld quality.
How does equipment care influence the overall productivity and longevity of mobile welding machines, and why is it important to affect weld quality?
Proper equipment care is essential for maintaining the productivity and longevity of mobile welding machines. When you take the time to ensure that your equipment is well-maintained, you can significantly affect weld quality, leading to more consistent and reliable welds. Moreover, incorporating routine checks and maintenance practices allows you to learn about potential issues before they escalate, ensuring that your welding operations run smoothly.
How can users learn about the importance of equipment care in maintaining mobile welding machines?
To learn about the importance of equipment care, users should familiarize themselves with routine maintenance practices that ensure optimal performance and longevity of mobile welding machines. Proper equipment care not only prolongs the life of the machines but also improves the quality of welds produced.
How can professionals learn about proper equipment care techniques to maintain mobile welding machines effectively?
Professionals can learn about equipment care through various resources such as training programs, manufacturer guidelines, and online tutorials that emphasize the importance of maintaining mobile welding machines for optimal performance.
How can technicians learn about the best techniques for equipment care for mobile welding machines?
Technicians can learn about equipment care through various resources such as workshops, online courses, and instructional videos that focus on maintaining mobile welding machines effectively. Understanding these techniques is crucial for ensuring optimal performance and reliability in welding jobs.
How can users learn about best practices in equipment care for mobile welding machines?
Users can learn about equipment care through various resources such as online tutorials, manufacturer manuals, and specialized training workshops that focus on maintaining mobile welding machines effectively.
How can users learn best practices in equipment care for mobile welding machines?
Users can learn best practices in equipment care for mobile welding machines by attending workshops, accessing online resources, and participating in training programs. These learning opportunities help users understand the importance of proper equipment care to enhance performance and longevity.
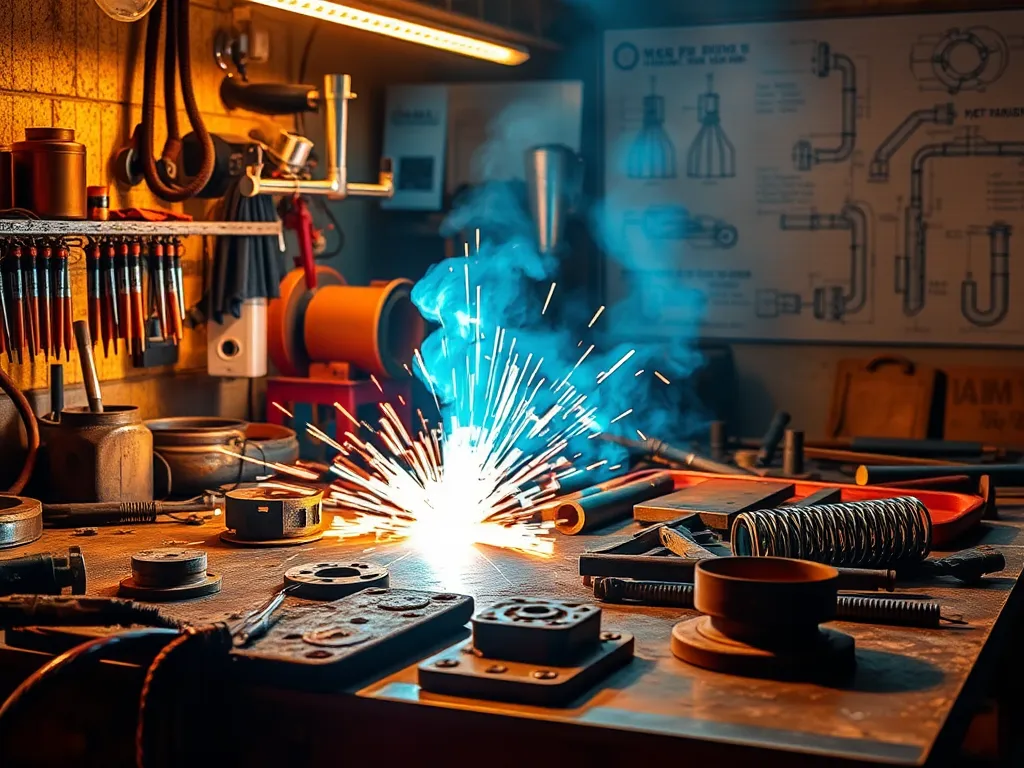
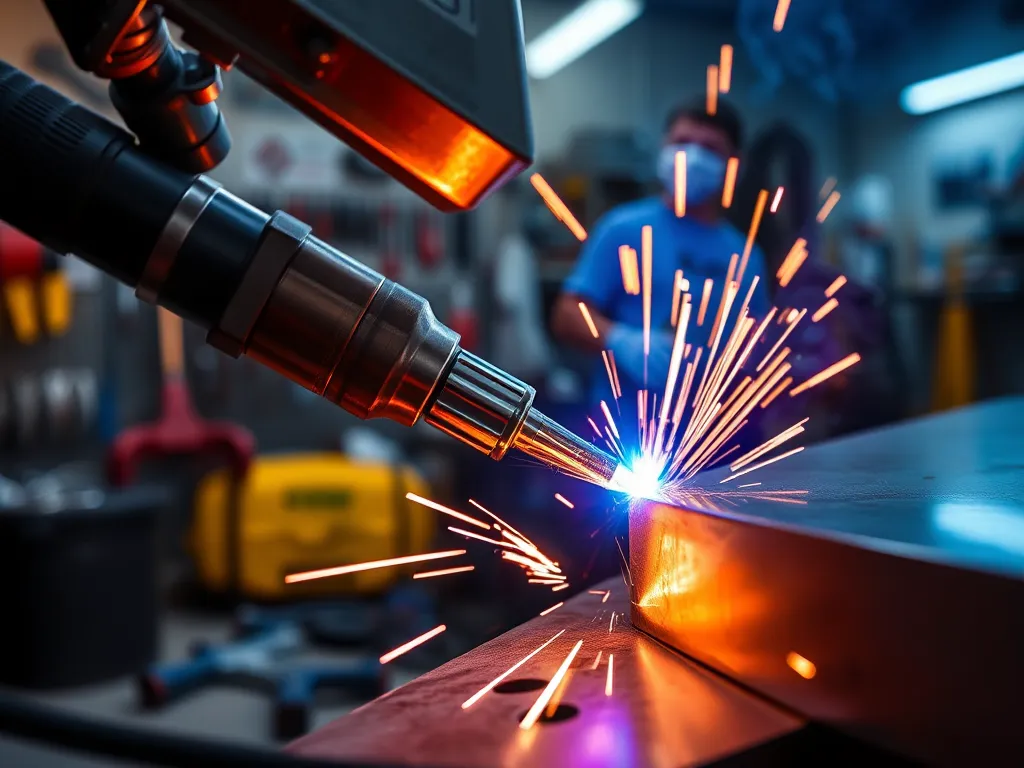
Discovering TIG Welding: Techniques, Benefits and Tips
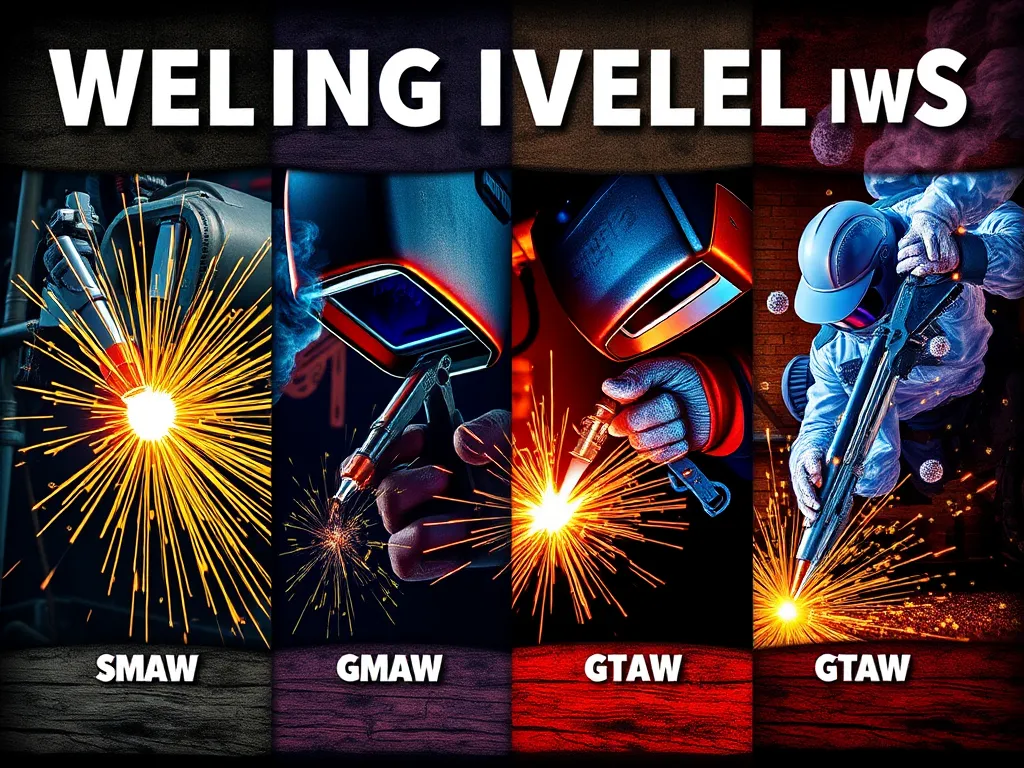
Exploring the 4 Major Categories of Welding Techniques
